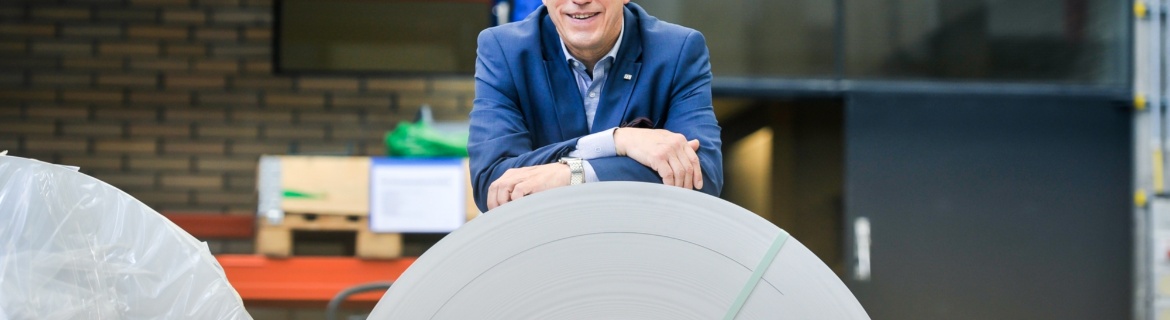
The Stuttgart Center for Manufacturing Technologies (PZS) has been combining the individual strengths of twelve Institutes from four faculties with a total of 400 research staff since 2017. As Prof. Mathias Liewald, head of the University of Stuttgart’s Institute for Metal Forming Technology (IFU) and spokesman for the PZS explains: "Due to the research they carry out in the field of production and information technology, PZS Institutes have had a visible profile for years.
Our scientific work is focused on the technological processes of various manufacturing methods, production flows and value creation chains. Our objective,” he continues, “is to work on future technologies and to take part in corresponding global developments that will eventually be adopted by companies within five to ten years." This objective, he says, is reflected in three fields of research: the optimization of value creation chains in a production setting in the context of resilient and circular value creation: the use of artificial intelligence (AI) methods in production, and finally sustainability, resource efficiency and climate neutrality.
The role of people in logistics processes
For example, two projects relating to inter-logistics and intralogistics, i.e., the global movement of goods between companies or within a company respectively, are focused on the role of people in the relevant logistics processes, because due to their cognitive abilities and high degree of flexibility, especially when it comes to picking goods, humans are indispensable in these processes. The "FlexLight" project is aimed at achieving a step-by-step improvement of manual picking performance through the use of a flexible pick-by-light system whereby rather than working with a packing list, the desired goods are visually displayed to the picker directly at the storage location. Conventional picking methods are rigid and, by definition, inflexible. The new approach, on the other hand, can independently expand itself and the system can be designed for specific applications. The project objective is to achieve an easy integration or adaptation of the picking method in changing environments. ThingOS GmbH, a spin-off of the University of Stuttgart, is our research partner in this project.
The "S³ - Safety Sensor Technology for Service Robots" project is our second example from the field of production logistics and involves research being carried out by the Institute of Mechanical Handling and Logistics (IFT) into the development of safe 3D environment sensor technology for use in mobile robots. Our project partners are Alexander Thamm GmbH, Pilz GmbH & Co. KG, the Fraunhofer Institute for Manufacturing Engineering and Automation IPA, and the BruderhausDiakonie of the Gustav Werner Foundation, and Haus am Berg. The aim is to develop sensor technology that is capable of reliably monitoring the environment in three dimensions, distinguishing between people and objects, and detecting irregularities.
The Institute for Manufacturing Technologies of Ceramic Components and Composites (IFKB) has also been a partner of the PZS since its foundation and collaborates with us on such things as the "KeraBear” project, which is funded by the state of Baden-Württemberg. The project was developed among a network of research partners all working in the field of production technology including Furtwangen University and the Fraunhofer Institute for Mechanics of Materials IWM in Freiburg. The goal of the project partners is to develop an innovative coating system for friction bearings to replace the materials commonly used today, because whilst these perform very well, they contain tungsten, cobalt and nickel – all heavy metals, which are considered problematic from an environmental and political perspective. Our current task is to qualify relatively new and harmless carbide and oxide ceramic materials for use in friction bearings. The coating process we use, which was developed at the IFKB, is known as high-speed suspension flame spraying.
Sustainable production processes
The Institute of Laser Technologies (IFSW) is also involved in the PZS network and deals specifically with potential future laser applications for things such as a machining tool, whereby they opt for a holistic approach developing and researching laser-based manufacturing processes, suitable beam sources and the necessary plant and system engineering processes.
"Two other key research fields have recently been established at the University of Stuttgart in collaboration with the Fraunhofer Society,” says Liewald, “both of which relate directly to future production technologies: one concerns the sustainability and resource efficiency of production processes, whilst the other involves the broad field of AI in production technology. We at the PZS benefit greatly from the work being carried by researchers in both fields with their specific expertise and networks."
The Institute for Energy Efficiency in Production (EEP), for example, coordinates the "Synergy” Copernicus project, which is part of the German Federal Ministry of Education and Research’s (BMBF) largest energy research initiative. The objective of the project is to adapt industrial energy demand to the increasingly volatile supply of renewable energy. Various approaches are being investigated by over 80 partners to specifically manage the industry's electricity needs without having a negative impact on product quality or delivery schedules. Thus far, a total flexibility capacity in the order of three nuclear power plant capacities has been identified and developed for German industry.
Increasing energy efficiency is a key pillar in the energy transition. The EEP collaborated in the "ACE - Asset Class Energy Efficiency” project with the Klimaschutz- und Energieagentur Baden-Württemberg GmbH (Baden-Württemberg Climate Protection and Energy Agency) and the German Industry Initiative for Energy Efficiency (DENEFF) to find out how investments in industrial energy efficiency could be financed more easily, because within companies such investments are always in competition with strategic investments in actual value creation. The requirements of the financial sector, energy service providers and manufacturers were analyzed in the course of the project. The project findings are set out in a project planning guide, which the German Federal Ministry for Economic Affairs and Energy (BMWi) will be able to expand upon to increase industrial energy efficiency.
Using artificial intelligence to program robots
A collaboration between the Fraunhofer IPA and the Institute of Industrial Manufacturing and Management (IFF) is an example of a PZS project involving AI: the "Rob-aKademI" project, which has just recently been completed, looked into the expertise required to program a robot to automate industrial handling or assembly processes. "Machine learning initiatives such as these will become much more important in production engineering in the near future," says Liewald. The robot can be programed with no manual intervention by combining a powerful physics simulation with so-called "Reinforced Learning", which is a special case of machine learning. The robot can even perform complex, force-controlled assembly operations "itself". This methodology is currently being studied and tested in practice in collaboration with industry partners based on switch assembly and circuit board component installation processes.
Optimizing the forging process
The Institute for Metal Forming Technology (IFU), the Institute of Industrial Automation and Software Engineering (IAS) and various industrial partners recently completed another project involving AI, the objective of which was to design a forging process of exemplary efficiency. Forging involves heating solid materials to high temperatures and then pressing them into the desired shape in a die or mold. The microstructure of the material can be adjusted by means of controlled cooling, for example, to achieve the desired strength of the component. Numerical simulations are usually used to calculate such forging processes in order to subsequently qualify them for a real-world series production ramp-up with no loss of time or test phases. Unfortunately, simulations and reality often diverge: in extreme cases, the simulation indicates that the component will fail, whereas it is not so bad in reality or vice versa. "Therefore,” as Liewald explains, ”we were faced with the scientific challenge of studying production and simulation data to gain specific insights in order to be able to use a neural network to compensate for fluctuating process conditions in terms of the expected component quality.”
An IFU team is now transferring this approach to series production start-up processes in cold forming, which is used to manufacture such things as gears or hollow shafts for lightweight construction. "In this project,” says Liewald, “the production start-up phase is, as it were, moved to a steady state as efficiently as possible, the objective being to largely eliminate so-called startup scrap,”. This significantly reduces the effort required – and therefore the costs – especially for small batches. mv
The twelve PZS institutes
- Institute of Electrical Energy Conversion (IEW)
- Institute for Energy Efficiency in Production (EEP)
- Institute for Manufacturing Technologies of Ceramic Components and Composites (IFKB)
- Institute of Aircraft Design (IFB)
- Institute of Mechanical Handling and Logistics (IFT)
- Institute of Industrial Manufacturing and Management (IFF)
- Institute of Parallel and Distributed Systems (IPVS)
- Institute for Control Engineering of Machine Tools and Manufacturing Units (ISW)
- Institute of Laser Technologies (IFSW)
- Institute of Applied Optics (ITO)
- Institute for Metal Forming Technology (IFU)
- Institute for Machine Tools (IfW)
Prof. Dr. Mathias Liewald, Director of the Institute for Metal Forming Technology (IFU), e-mail, phone: +49 711 685 83840