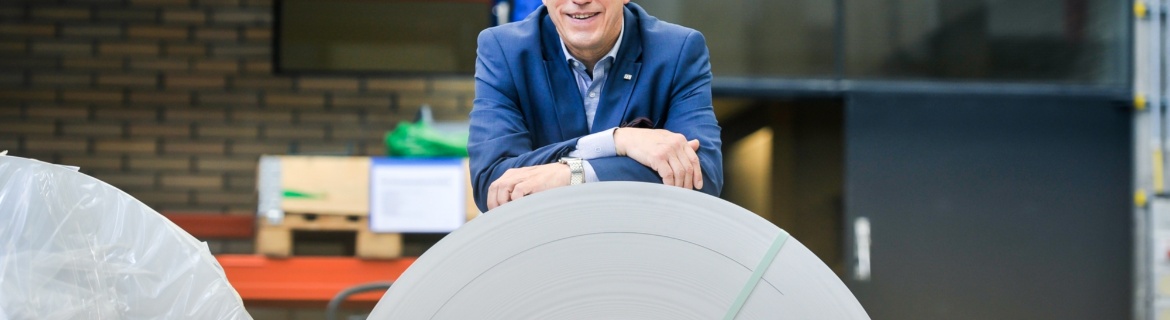
Seit 2017 bündelt das Produktionstechnische Zentrum Stuttgart (PZS) die spezifischen Stärken von zwölf Instituten aus vier Fakultäten mit insgesamt 400 wissenschaftlichen Mitarbeiterinnen und Mitarbeitern. „Die Institute des PZS sind mit ihrer Forschungsarbeit auf dem Gebiet der Produktions- und der Informationstechnik seit Jahren sichtbar“, sagt Prof. Mathias Liewald, Leiter des Instituts für Umformtechnik (IFU) an der Universität Stuttgart und Sprecher des PZS.
„Im Mittelpunkt unserer wissenschaftlichen Arbeiten stehen technologische Prozesse verschiedener Fertigungsverfahren, Produktionsabläufe und Wertschöpfungsketten. Unser Ziel ist es, an Zukunftstechnologien zu arbeiten und an entsprechenden weltweiten Entwicklungen mitzuwirken, die dann mit einem Zeithorizont von fünf bis zehn Jahren Einzug in die Unternehmen halten.“ Dieser Anspruch schlage sich in drei Forschungsfeldern nieder. Erstens: der Optimierung von Wertschöpfungsketten in der Produktion im Rahmen einer resilienten und zirkulären Wertschöpfung, zweitens: dem Einsatz von Methoden Künstlicher Intelligenz (KI) in der Produktion sowie drittens: dem Themenbereich Nachhaltigkeit, Ressourceneffizienz und Klimaneutralität.
Die Rolle des Menschen in Logistikprozessen
So geht es bei zwei Projekten aus der Inter- und Intralogistik, also der globalen Bewegung von Gütern zwischen Unternehmen beziehungsweise innerhalb eines Betriebsgeländes, um die Rolle des Menschen in diesen Logistikprozessen. Schließlich ist der Mensch dabei aufgrund seiner kognitiven Fähigkeiten und seiner hohen Flexibilität unverzichtbar, speziell in der Kommissionierung von Waren. Im Projekt „FlexLight“ wird die schrittweise Verbesserung der manuellen Kommissionierleistung anhand eines flexiblen Pick-by-light-Systems weiterentwickelt. Bei diesem Ansatz arbeitet der Kommissionierer ohne Packliste, stattdessen werden ihm die gewünschten Güter direkt am Lagerort visuell angezeigt. Konventionelle Kommissioniermethoden sind starr und damit unflexibel. Dagegen erweitert sich der neue Ansatz selbstständig oder lässt sich anwendungsspezifisch ausgestalten. Ziel des Projekts ist es, eine einfache Integration oder Adaption der Kommissioniermethode in sich verändernden Umgebungen zu erreichen. Forschungspartner ist die ThingOS GmbH, eine Ausgründung der Universität Stuttgart.
Das zweite Beispiel aus der Produktionslogistik ist das Projekt „S³ – Sicherheitssensorik für Serviceroboter“. Dabei forscht das Institut für Fördertechnik und Logistik (IFT) an der Entwicklung einer sicheren 3D-Umgebungssensorik für den Einsatz in mobilen Robotern. Partner sind die Alexander Thamm GmbH, die Pilz GmbH & Co. KG, das Fraunhofer-Institut für Produktionstechnik und Automatisierung IPA sowie die BruderhausDiakonie der Stiftung Gustav Werner und Haus am Berg. Die zu entwickelnde Sensorik soll die Umgebung dreidimensional sicher überwachen, zwischen Personen und Objekten unterscheiden sowie Unregelmäßigkeiten erkennen können.
Das Institut für Fertigungstechnologie keramischer Bauteile (IFKB) gehört ebenfalls seit der Gründung des PZS zu dessen Partnern, zum Beispiel mit dem Verbundvorhaben „KeraBear“, das durch das Land Baden-Württemberg gefördert wird. Das Projekt entstand in einem Netzwerk von produktionstechnisch arbeitenden Forschungspartnern wie der Hochschule Furtwangen und dem Fraunhofer-Institut für Werkstoffmechanik IWM in Freiburg. Die Projektpartner wollen ein innovatives Schichtsystem für Gleitlager entwickeln, durch das sich die heute gebräuchlichen Werkstoffe ersetzen lassen. Letztere sind zwar sehr leistungsfähig, enthalten aber Wolfram, Cobalt und Nickel – Schwermetalle, die in umwelttechnischer und politischer Hinsicht als problematisch gelten. Die Aufgabe besteht nun darin, relativ neue und unbedenkliche karbidische und oxidkeramische Werkstoffsysteme für die Anwendung in Gleitlagern zu qualifizieren. Als Beschichtungsverfahren kommt das am IFKB entwickelte Hochgeschwindigkeits-Suspensionsflammspritzen zum Einsatz.
Nachhaltigkeit in Produktionsprozessen
Auch das Institut für Strahlwerkzeuge (IFSW) wirkt im Netzwerk des PZS mit, konkret an den zukünftigen Einsatzmöglichkeiten des Lasers, zum Beispiel als Bearbeitungswerkzeug. Das IFSW wählt dabei einen ganzheitlichen Ansatz: Es entwickelt und untersucht laserbasierte Fertigungsverfahren, dafür geeignete Strahlquellen sowie die erforderliche Anlagen- und Systemtechnik.
„In den letzten Jahren wurden an der Universität Stuttgart zusammen mit der Fraunhofer-Gesellschaft zwei weitere wesentliche Forschungsfelder im unmittelbaren Kontext zukünftiger Produktionstechnologien etabliert: die Nachhaltigkeit von Produktionsprozessen und deren Ressourceneffizienz sowie der weite Bereich der KI in der Produktionstechnik“, so Liewald. „Beide Felder nutzen uns im PZS mit ihren Kompetenzen und Netzwerken erheblich.“
So koordiniert zum Beispiel das Institut für Energieeffizienz in der Produktion (EEP) das Kopernikus-Projekt „Synergie“. Dieses Projekt bildet einen Teil der größten Energieforschungsinitiative des Bundesministeriums für Bildung und Forschung (BMBF). Es hat zum Ziel, die industrielle Energienachfrage dem zunehmend volatilen Angebot Erneuerbarer Energien anzupassen. Mit mehr als 80 Partnern werden unterschiedliche Ansätze untersucht, um den Strombedarf der Industrie ohne negative Auswirkungen auf Produktqualität oder Liefertermine gezielt zu steuern. Insgesamt wurden für die deutsche Industrie bislang Flexibilitäten in der Größenordnung von drei Atomkraftwerkskapazitäten identifiziert und entwickelt.
Die Steigerung der Energieeffizienz ist eine wesentliche Säule der Energiewende. Zusammen mit der Klimaschutz- und Energieagentur Baden-Württemberg und der Deutschen Unternehmensinitiative Energieeffizienz arbeitete das EEP in dem Projekt „ACE – Asset Class Energy Efficiency“ daran, wie Investitionen in industrielle Energieeffizienz leichter zu finanzieren sind, denn diese stehen in den Unternehmen stets im Wettbewerb zu strategischen Investitionen in die Wertschöpfung selbst. Hierbei wurden die Anforderungen der Finanzbranche, von Energiedienstleistern und von produzierenden Unternehmen analysiert. Ein Projektierungsleitfaden stellt die Erkenntnisse dieses Projektes bereit, auf dem das Bundesministerium für Wirtschaft und Energie (BMWi) aufbauen kann, um die industrielle Energieeffizienz zu steigern.
Roboter programmieren mittels Künstlicher Intelligenz
Ein Beispiel für ein PZS-Projekt aus dem Gebiet der KI ist eine Kooperation des Fraunhofer IPA in Zusammenarbeit mit dem Institut für industrielle Fertigung und Fabrikbetrieb (IFF). „Solche Initiativen zum maschinellen Lernen in der Produktionstechnik werden in den nächsten Jahren stark an Bedeutung gewinnen“, sagt Liewald. Das soeben abgeschlossene Projekt „Rob-aKademI“ befasste sich mit dem Expertenwissen für die Programmierung eines Roboters zur Automatisierung von industriellen Handlings- oder Montageprozessen. Durch die Kombination einer leistungsstarken Physiksimulation mit dem sogenannten „Reinforced Learning“, einem Spezialfall des maschinellen Lernens, wird es möglich, den Roboter ohne manuellen Eingriff zu programmieren. Selbst komplexe, kraftgeregelte Montageoperationen kann der Roboter „selbst“ ausführen. Diese Methodik wird aktuell mit Industriepartnern anhand der Montage von Schaltern sowie dem Bestücken von Platinen untersucht und praktisch erprobt.
Den Schmiedeprozess optimieren
Ein weiteres Projekt, in dem KI eine Rolle spielt, hat das Institut für Umformtechnik (IFU) kürzlich gemeinsam mit dem Institut für Automatisierungstechnik und Softwaresysteme (IAS) und Industriepartnern abgeschlossen. Es ging darum, beispielhaft einen möglichst effizienten Schmiedeprozess zu gestalten. Schmieden heißt, dass Vollmaterial auf hohe Temperaturen erhitzt und anschließend in einem Werkzeug in die gewünschte Form gepresst wird. Durch ein gesteuertes Abkühlen lässt sich die Mikrostruktur des Materials einstellen, um zum Beispiel die gewünschte Festigkeit des Bauteils zu erzielen. Üblicherweise berechnet man solche Schmiedeprozesse mit numerischen Verfahren, um sie anschließend in der Realität für den Serienhochlauf ohne Zeitverluste und Testphasen zu qualifizieren. Leider liegen Simulation und Realität oftmals auseinander: Im Extremfall besagt die Simulation, dass das Bauteil versagen wird, während es in der Realität gar nicht so schlecht ist – oder umgekehrt. „Somit ergab sich für uns die wissenschaftliche Aufgabenstellung, aus Produktions- und Simulationsdaten gezielt zu lernen, um mit einem neuronalen Netz schwankende Prozessverhältnisse in Bezug auf die zu erwartende Bauteilqualität zu kompensieren“, erklärt Liewald.
Diesen Ansatz überträgt ein IFU-Team nun auf Serienanlaufprozesse in der Kaltumformung. Mit diesem Umformverfahren werden beispielsweise Zahnräder oder Hohlwellen für den Leichtbau hergestellt. „In diesem Projekt wird der Produktionsanlauf sozusagen möglichst effizient in einen stabilen Zustand überführt, um den sogenannten Anfahrausschuss weitgehend zu vermeiden“, sagt Liewald. Das senkt den Aufwand – und damit die Kosten – deutlich, besonders bei kleinen Stückzahlen. mv
Die zwölf Institute des PZS:
- Institut für Elektrische Energiewandlung (IEW)
- Institut für Energieeffizienz in der Produktion (EEP)
- Institut für Fertigungstechnologie keramischer Bauteile (IFKB)
- Institut für Flugzeugbau (IFB)
- Institut für Fördertechnik und Logistik (IFT)
- Institut für Industrielle Fertigung und Fabrikbetrieb (IFF)
- Institut für Parallele und Verteilte Systeme (IPVS)
- Institut für Steuerungstechnik der Werkzeugmaschinen und Fertigungseinrichtungen (ISW)
- Institut für Strahlwerkzeuge (IFSW)
- Institut für Technische Optik (ITO)
- Institut für Umformtechnik (IFU)
- Institut für Werkzeugmaschinen (IfW)
Prof. Dr. Mathias Liewald, Institutsdirektor Institut für Umformtechnik E-Mail, Telefon: +49 711 685 83840