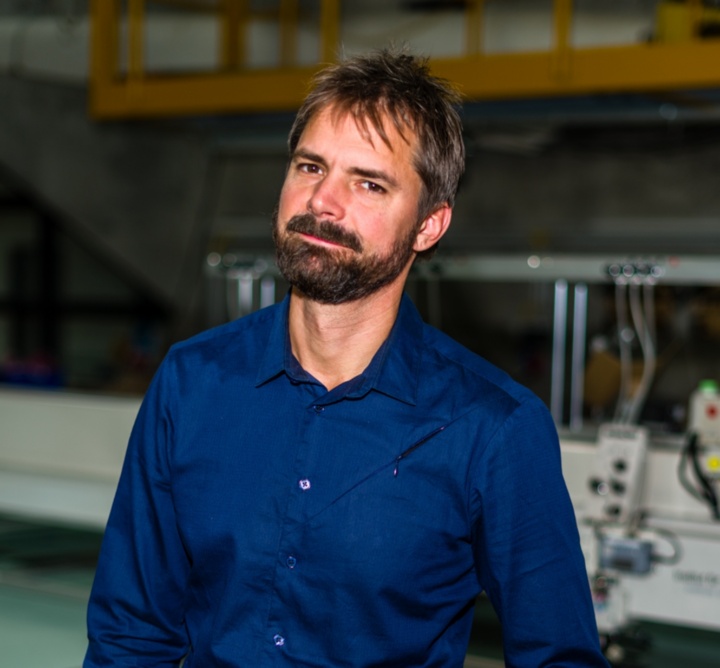
Aircraft components, lamps, gnomes, loudspeakers, orthoses, rings – and that’s not all. At Innfa GmbH, versatility in the use of high technology has been a major priority since 2012. Fiber composite materials form the basis of all the creative ideas with which the company founders Markus Blandl, Gerd Falk and Steffen Müller develop special solutions to the various problems of their customers.
Both Innfa CEOs Blandl and Falk initially worked at the Institute of Aircraft Design at the University of Stuttgart. They scaled down their activities as members of staff some time ago, and now contribute their know-how in matters related to lightweight construction and fiber composites at their own company and to research.
Impregnation ensures new possible applications
The enormous range of possible uses of fiber composite materials is the work of Blandl and Falk. If lightweight and space-saving materials are required which are also robust, such as in the aircraft and car manufacturing industries, these high-tech materials have already become established. The focus of the Innfa founders is on what this can achieve in previously unexplored territory, such as in acoustics or lighting systems. It suits the creativity of the two founders to develop new technology specifically for the purpose. This technology can be used to impregnate the carbon fibers quickly and easily without the need for complex technical equipment, and when being unrolled from the coil afterwards the carbon fibers are easy to process in any desired form.
New technology stops carbon fibers from becoming brittle
By using so-called T-Preg technology, the inventors have built a car body for their appearances at trade fairs among other things, and the gnomes for the Federal Garden Show in Heilbronn were also made using this technology. “Using our technology means that there are no brittle dry spots on the carbon fibers which break easily”, emphasizes Gerd Falk, and adds: “The process is also clean, and we have been able to significantly reduce the processing costs.” Their technology is currently also in demand for manufacturing hydrogen tanks, since it enables a more lightweight construction with thinner walls at a lower cost.
Enthusiasm for high-tech materials
“DIY” is the name of the game for Markus Blandl and Gerd Falk. When they set up their company they decided not to accept funding. However, they were happy to accept tips and advice from the University of Stuttgart initiative Technologie-Transfer-Initiative GmbH – one of two contact points for members of the university who are interested in setting up their own company. The founders would have been able to branch out and work with interested partners by this stage. “This would have meant that we would have had to fully concentrate on a project though and put everything else on hold”, says Markus Blandl. They aren’t quite at that stage yet, says Blandl, but he believes that they may be able to compete on the market anyway. Blandl says that it isn’t easy to decide between coils, lamps, loudspeakers and the like in particular, and having the freedom to explore what is possible using the exciting properties of carbon fibers thanks to the wide variety of clients is a lot of fun.
“It’s great – you can do everything with carbon fibers”
Markus Blandl, wissenschaftlicher Mitarbeiter am IFB und Geschäftsführer der Innfa GmbH
For example, carbon fibers can conduct electricity, which Falk and Blandl use on a super-lightweight filigrane lamp which is inspired by a leaf. The fibers embroidered on a carrier surface become brilliant leaf veins thanks to the LEDs stuck onto it. “It’s great – you can do everything with carbon fibers”, says an enthusiastic Markus Blandl. Its high level of rigidity means it can transport sound waves with almost no loss. This means a simple shoebox can be made into an impressive surround system, together with vibro speakers and Bluetooth control. Bango is the name for the distinctive loudspeaker sticking to a wall inside the box, which looks like a six-legged spider. “Our carbon spider is ideal for all kinds of events, since it turns a cardboard box which is easy to transport into a loudspeaker with optimum sound quality. It’s also low on electricity consumption”, says Gerd Falk. “With our own products and developments such as the Bango, we try, above all, to focus on the enormous advantages of fiber composite technologies even in previously unknown areas of application such as acoustics,” says Markus Blandl. “With our own products and developments such as the Bango, we try, above all, to focus on the enormous advantages of fiber composite technologies even in previously unknown areas of application such as acoustics,” says Markus Blandl.
Initiatives for those wanting to start up their own company
Those who are interested in setting up their own company can get in touch with the TTI, or those who are looking for an initial consultation in particular can get in touch with the Exi+ project based at the Institute for Entrepreneurship and Innovation Science.
Applying for a patent
To impregnate the fiber, the researchers prepared the patent application together with the Knowledge and Technology Transfer Department from Division 1. This patent forms the basis of a number of orders, and has been applied for by the university for several European countries as well as the USA.