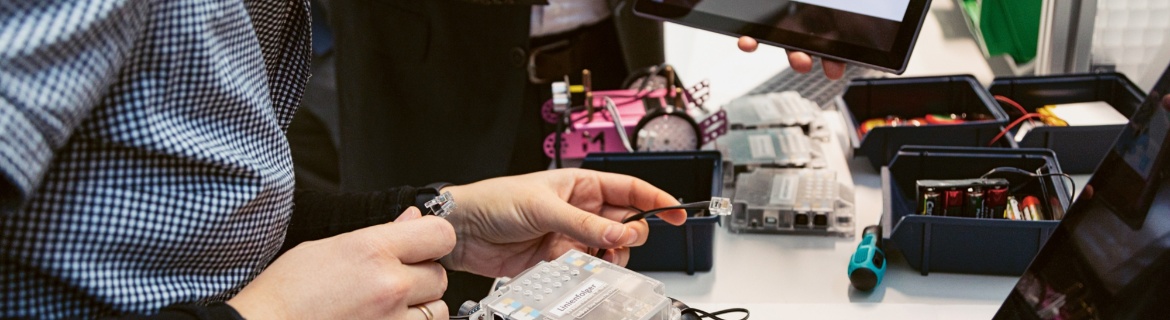
Individualization is a mega trend that is having a decisive effect on contemporary society, which is evident, for example, in the increased demand for bespoke products and services. How can companies find out whether personalized production would be worth their while? How can they adapt products or services to individual needs and still manufacture things in a cost-effective manner?
The Mass Personalization High Performance Center [DE] is a joint initiative of the University of Stuttgart and the Stuttgart-based Fraunhofer Institutes. Researchers there are developing interdisciplinary and cross-sector methods, procedures, processes, production systems and business models for the creation of bespoke products. "Mass personalization" involves a new, holistic product manufacturing approach, as Prof. Peter Middendorf, spokesman for University of Stuttgart’s High Performance Center explains. The users are the main focus and the bespoke products and services do not cost much more than mass-produced goods.
“Our current production technology is geared up for efficiency and is based mainly on achieving a high degree of product uniformity, which is the credo of mass production. And this is important because it gives us cheap products. So, among other things, manufacturing bespoke goods for the masses will require new manufacturing technologies."
Bespoke medical engineering products
o bring basic fabrication research and biomaterial technologies for bespoke biomedical systems together, the University of Stuttgart founded a Stuttgart Partnership Initiative, in which nine University Institutes are currently participating. "
Bespoke medical technology is urgently needed from a patients' perspective, because humans are not standardized off-the-shelf products," says Prof. Günter Tovar [DE], the spokesman of the initiative.
Bespoke medical engineering promises a long-term, sustainable use in future healthcare and therapy. Several University of Stuttgart Institutes are carrying out collaborative research with the Fraunhofer Society, into such things as bespoke corsets and cartilage implants. Dr. Okan Avci, Deputy Head of Department for Biomechatronic Systems at the Fraunhofer Institute for Manufacturing Engineering and Automation (IPA), and his team are developing digital networks, business models and data systems in addition to setting up digitized medical engineering processes without which, a cost-efficient production of bespoke products would not be possible.
"In addition to orthopedic technicians,” as Avci explains, “there isa plethora of specialists employed in the field of medical engineering, such as mensuration technicians, IT experts and simulation engineers, all of whom are needed, forexample, to analyze the effectiveness and wearing comfort of a bespoke scoliosis corset, to test its stability and to produce it at a cost-effective price." The work involved is extremely time-consuming and expensive and yet, as Avci goes on to say, these corsets, which are required exclusively by children and adolescents, are often clunky, stiff, oversized and uncomfortable.
That is why Avci and his colleagues are developing a virtual testing system for people who need a scoliosis corset to correct their spinal curvature, which will enable patients to try on a virtual version of the corset first. This involves simulating such things as height and movement behavior data to illustrate how the corset will behave when the respective patient moves. "We enter the data from the corset and the human into our virtual testing system, which computes and optimizes the data and shows us what the final corset should be like for each patient to optimize freedom of movement, eliminate pressure points and still be sufficiently stable."
Bone-cartilage implants made of biomaterials
The additive manufacturing of personalized products relies on data from detailed analyses. Another project currently being run at the Mass Personalization High Performance Center is focused on the additive manufacturing of personalized cartilage implants. Osteoarthritis of the knee can be caused by misalignment, obesity or competitive sports and patients suffer from pain and restricted mobility. The project is aimed at the development of an end-to-end automated process chain from the CT scan to the bespoke implant, facilitated by a comprehensive process optimization.
The project is being supervised by Frederik Wulle of the University of Stuttgart’s Institute for Control Engineering of Machine Tools and Manufacturing Units (ISW) and his colleagues, who are investigating ways of manufacturing bespoke biological bone-cartilage implants from biomaterials in an automated manner. Wulle is responsible for the additive manufacturing of the implants using 3D printing technology.
"We generate the geometry to be printed on the basis of the biomechanical data and the reconstruction geometry." The necessary data is supplied by colleagues at the IPA, where researchers use analysis data of the musculoskeletal system to derive information about such parameters as the requisite size and stiffness of the bespoke cartilage implants so that they optimally match the patient’s individual biology and biomechanics and enable a successful course of therapy.
Wulle and his colleagues use this data to reconstruct the nominal geometry of the defective body part to be replaced using computer-aided design technology. Additive manufacturing processes are used to construct objects with a correspondingly complex geometry from different materials. To manufacture the cartilage implants the team relies on innovative multi-axis 3D printing and machining technology, the advantage of which is greater process freedom compared to the conventional three-axis process. It can, for example, minimize the step effect that happens when a component contour is not parallel or orthogonal to the build direction, which subdivides the slope into discrete layers.
Interdisciplinary collaboration
The bone-cartilage implants used in the project are made of biomaterials. The ultimate goal of the interdisciplinary field of bioprinting is to produce biomimetic tissue structures as replacements for the patients’ diseased tissue, whereby they orient themselves on the biological tissue and attempt to use digital printing processes to reproduce it. The biomaterials in question are developed, produced and tested at the Institute of Interfacial Process Engineering and Plasma Technology (IGVP) and the Fraunhofer Institute for Interfacial Engineering and Biotechnology (IGB) in Stuttgart. Commenting on the interdisciplinary collaboration, Wulle explains that "we had developed the multi-axis 3D printing technology and were searching for an application when our materials development colleagues recognized its potential for their own application.”
Would it be worth our while?
Ever more companies are responding to the bespoke manufacturing trend, which is why The High Performance Center is offering targeted training programs [DE] for them. "Entering into a collaboration with us gives a company access to multifaceted expertise that is otherwise hardly accessible,” says the spokesman for the High Performance Center, Peter Middendorf: “Potential collaboration partners can use it to approach future technologies.”
Lesley-Ann Mathis and her colleagues at the University of Stuttgart’s Institute of Human Factors and Technology Management (IAT) have developed a method with which companies can systematically analyze their product portfolio for personalization potential to decide whether bespoke product development would be worthwhile for them. She and her team teach their method to companies in the context of continuing education seminars presented at the High Performance Center. They then offer companies a potential analysis for their specific product sets or servicesin follow-up projects.
The method they have developed is based on the so-called "product journey" and "user journey". As Mathis explains: "We take a user-centric approach in the High Performance Center: our approach starts directly with the user." To illustrate her process she uses the example of an e-scooter that can be rented via an app for a certain time and distance. During the so-called product journey, she and the seminar participants analyze the group at which the product will be targeted throughout its entire life cycle and which user groups would come into contact with the product.
In the case of the e-scooter, these might include university students who would use it to travel to their next lecture, or employees who would use it to travel from the train station to the office. But the wider range of user groups includes the people who pre-assemble them, pick them up and transport them to collection points, or ultimately recycle them. This creates so-called protopersonas, such as Colin Commuter or Sandra Student, within the product journey, whose surnames obviously represent their primary characteristics.
To map out the user journey, one of the primary target groups for the product is selected after which the seminar participants accompany, for example, Sandra Student during her entire contact with the e-scooter from when she first books it via the app to when she parks it up and leaves it. "We analyze where the user comes into direct contact with the product and assess how the user experience could be improved and where opportunities for personalization might exist," Mathis explains.
All ideas are first analyzed in terms of their benefit to the user before being subjected to a cost-benefit analysis. Remaining with the example of the e-scooter, it might be possible to develop a personalized voice response system that would render the use of the smartphone app obsolete, or provide personalized pricing models for regular users and frequently used routes.
The holistic approach would benefit companies in various ways says Mathis: "We use a specific tool to identify relatively quickly and at an early product development stage whether a product is suitable for personalization and whether it would be worthwhile." After all, bespoke products will only be successful if they really do benefit the customer.
Editor: Bettina Wind
Prof. Peter Middendorf, University of Stuttgart, phone: +49 711 685-62411, e-mail