Styrofoam, food packaging, foams or construction elements: many products contain mixed plastic. “At the end of their life cycle, these products become problematic waste,” says Hannah Storm, doctoral researcher at the Institute of Combustion and Power Plant Technology (IFK) at the University of Stuttgart.
The term mixed plastic covers composite materials made from different types of plastic. These cannot yet be collected and sorted by type and are difficult to recycle. Researchers from the Institute of Bioprocess Engineering and the Institute of Combustion and Power Plant Technology (IFK) at the University of Stuttgart, in collaboration with colleagues from the University of Ulm, aim to change this. The interdisciplinary team is developing a new process to extract recyclable materials for the chemical industry from mixed plastics.
Circular economy: recovering recyclable materials from waste
“Our approach involves two stages,” explains Russell Ngo, a doctoral researcher at the Institute of Bioprocess Engineering. "First, we apply a gasification process to decompose the mixed plastic into its basic molecular components. The second step is called gas fermentation: The gas mixture is utilized by anaerobic bacteria. These use special biochemical processes that we ultimately want to use to produce isobutanol, for example." Isobutanol is used in the chemical industry as a valuable material for a wide range of products, for example as a solvent in paints and varnishes or as an additive for de-icing agents, cleaning agents and polishes.
Two-stage process
Hannah Storm is responsible for the first process step, the gasification of the mixed plastics. The process engineer uses the fluidized bed system at the University of Stuttgart for her research. The test facility, standing over three meters tall, enables flexible testing of various combustion, gasification, and CO₂ capture technologies. “In the fluidized bed system, we heat the mixed plastic to over 700 °C and introduce steam to the process. This breaks down the long carbon chains in the plastics into their individual components. We end up with an energy-rich synthesis gas that consists of carbon monoxide and hydrogen, among other things,” says Storm. This synthesis gas is the starting product for the second process step, gas fermentation. “The goal of my doctoral research is to optimize the gasification process to produce the cleanest possible synthesis gas,” says Storm.
Chemical engineer Russell Ngo is responsible for gas fermentation. “The bacteria that utilize the synthesis gas feed on carbon dioxide, hydrogen and carbon monoxide,” says Ngo, who is currently testing various microorganisms to find out which strains are best suited to the process. He initially carries out small-scale experiments in gas-tight test tubes. If a bacterial strain shows promise, he proceeds with a series of tests in the bioreactor, an industrial-scale device where biological processes are carried out under controlled conditions. This allows him to carry out even more precise measurements.
The project is now entering the second stage
Before the process can be put into practice, there are still several challenges to address. “In the first year of the project, we demonstrated that the value chain holds significant potential,” says Prof. Ralf Takors, Head of the Institute for Biochemical Engineering. “As a result, the Baden-Württemberg Ministry of Science, Research and the Arts extended the project funding for a further three years. In the second phase, we want to optimize the two process steps of gasification and gas fermentation.”
To achieve this, Ngo and Storm will soon be receiving support from three other doctoral researchers. “I find it very motivating that my doctoral degree studies have such a direct practical benefit. And through my experiments on the fluidized bed system, I am learning a lot about the correct handling of large-scale plants,” says process engineer Storm. For chemical engineer Ngo, who moved from Singapore to Stuttgart for study for his doctoral degree, the interdisciplinary aspect is what makes the project so appealing: “Hannah and I work closely together. That’s why we don’t limit ourselves to our individual areas of expertise—we collaborate with a holistic view of the entire process chain. It’s an incredibly valuable learning experience."
Microorganisms as helpers in climate protection
Researchers from the Institute of Combustion and Power Plant Technology (IFK) at the University of Stuttgart and researchers from the University of Ulm are involved in the project “Mischkunststoffe: vom Problemfall zur Problemlösung durch Inwertsetzung mit Mikroorganismen (MiMiWin)” (Mixed plastics: from problem to solution through valorization with microorganisms). The research partners at the University of Ulm complement the collaboration by genetically optimizing microbes that metabolize and utilize the gas stream and produce isobutanol, as well as carrying out a life cycle analysis and a techno-economic analysis.
The project is funded under the initiative “Microorganisms as Helpers in Climate Protection – Harnessing Microbial Processes for a Climate-Neutral Future through Innovative Methods.” The Baden-Württemberg Ministry of Science, Research and the Arts supported nine projects for one year as part of this program. Four of them were recently extended for a further three years, including two projects at the University of Stuttgart: “MiMiWin” and the “SimBioZe” project, which is researching a “wastewater-bioconcrete-fertilizer” value chain.
The Stuttgart Way
The "Stuttgart Way" embodies a strong commitment to interdisciplinary research and teaching. The University of Stuttgart builds bridges between engineering, the natural sciences, the humanities, economics, and the social sciences. It promotes collaboration across institutional boundaries, encourages diverse perspectives, and places a strong emphasis on dialogue. Researchers, lecturers, and students benefit from an environment that fosters joint inquiry, collaborative problem-solving, and critical reflection on the societal impact of their work.
Contact
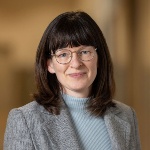
Lena Jauernig
Editor Research / Early Career Researchers