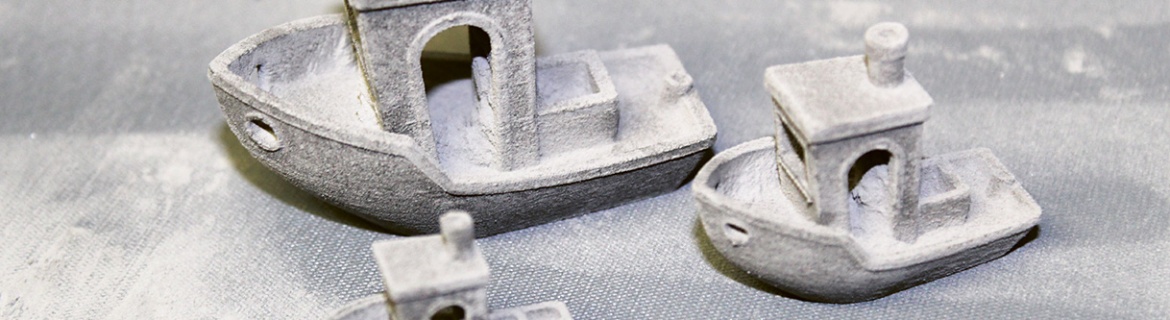
Hinter dem Begriff „additive Fertigung“ verbergen sich unterschiedliche Produktionsprozesse – doch alle haben eine Gemeinsamkeit: Im Gegensatz zur „substraktiven Fertigung“ oder Zerspanung entsteht ein Werkstück nicht, indem Material abgetragen wird, bis die gewünschte Form erreicht ist. Stattdessen werden auf Basis eines 3D-Modells Kunststoffe, Metalle, Keramiken oder Kunstharze computergesteuert Schicht für Schicht zu einem dreidimensionalen Teil aufgebaut. „Wir setzen im 3D-Druck möglichst nur so viel Material ein, wie wir wirklich brauchen, und wir bringen es genau an die richtige Stelle“, erläutert Dr. Alexander Geyer, Leiter der Verarbeitungstechnik am IKT.
Weniger Lagerhaltung und Logistik
Die additive Fertigung hat viele Vorteile. Nachbearbeitungsschritte entfallen weitgehend. Es entsteht weniger Ausschuss und der Materialverbrauch sinkt. Nahezu jedes Design und komplexe Geometrien werden möglich. Mittels 3D-Druck entstehen maßstabsgetreue Modelle, Werkzeuge oder auch Ersatzteile „on demand“, die direkt vor Ort gefertigt werden. Lagerhaltung und Logistik können damit zurückgefahren werden. Für die Massenfertigung eignen sich die nach wie vor langsamen Verfahren zwar nicht. Aber Branchen wie der Medizintechnik mit ihren patientennahen Produkten oder der Luft- und Raumfahrt, die auf Leichtbauteile aus Polymeren setzt, bieten sie neue Möglichkeiten.
Im Labor des IKT arbeiten die 3D-Drucker fast geräuschlos. Im Regal stehen die Ergebnisse der hier laufenden Experimente – von der Einlage für den Sportschuh über den Bremssattel für das Auto bis zum Modellschiff. Was auf den ersten Blick verspielt wirkt, dient der Grundlagenforschung. Geyer und sein Team sind auf der Suche nach innovativen Technologien, mit denen sie den 3D-Druck nachhaltiger gestalten können. Dabei nehmen sie unter anderem zwei Verfahren in den Fokus: das Selektive Lasersintern (SLS) und das Fused Deposition Modeling (FDM).
Beim SLS-Verfahren kommt ein Kunststoffpulver zum Einsatz, das feiner ist als Sand. Das Pulverbett wird in einem auf hohe Temperaturen erhitzten Bauraum an den Punkten aufgeschmolzen, die das 3D-Modell am Computer vorgibt. Anschließend wird das Pulverbett abgesenkt und die nächste, nur 100 Mikrometer dünne Schicht aufgetragen. Das umgebende Pulver stützt die Konstruktion, aus dem am Ende das Produkt leicht herausgelöst werden kann.
Altes Pulver recyceln
Das Problem: Im Falle des am häufigsten eingesetzten Kunststoffes werden rund 70 Prozent des Pulvers durch die hohen Temperaturen geschädigt. Um es dennoch wiederzuverwenden, wird es mit neuem Pulver vermischt. „Das hat zur Folge, dass die Qualität des Werkstoffes schwankt“, erklärt Dr. Sandra Weinmann, wissenschaftliche Mitarbeiterin am IKT. „Nachhaltiger ist es, das Pulver im laufenden Fertigungsprozess zu regenerieren.“ Dieses „Altpulverrecycling“ will die Chemikerin erreichen, indem sie die Pulverpartikel mit einem Modifikator kombiniert. Er soll dafür sorgen, dass die Schäden im Material direkt „repariert“ werden. Erste Versuche sind vielversprechend verlaufen. Jetzt geht es unter anderem darum, die optimale Rezeptur zu finden und die Anlagentechnik anzupassen.
Mit der Optimierung des FDM-Verfahrens wiederum beschäftigt sich Weinmanns Institutskollegin Silvia Lajewski. Hierbei wird ein Kunststoffstrang in einer beheizten Düse aufgeschmolzen und dann an vordefinierten Punkten auf eine Bauplattform aufgetragen. Problematisch sind die Strukturen, die im Fertigungsprozess durch ein zweites Material gestützt werden, um komplexe Geometrien mit beispielsweise starken Überhängen zu realisieren. Um sie nach dem Erstarren wieder zu entfernen, werden sie in der Regel in einem Wasserbad aufgelöst.
Wasserlösliches und biologisch abbaubares Stützmaterial
Dadurch gelangt jedoch schädliches Mikroplastik ins Abwasser. „Herkömmliche Kläranlagen können das nicht herausfiltern“, sagt Lajewski. Deswegen will sie ein Stützmaterial entwickeln, das wasserlöslich und zugleich biologisch abbaubar ist, indem es von Bakterien verstoffwechselt wird. Derzeit setzt sie auf einen Zwei-Komponenten-Werkstoff aus Polymer und einem hochfeinen Salz. Die Idee dahinter: Das Salz löst sich im Wasser aus den fertigen Strukturen, die dadurch so porös werden, dass man sie rückstandslos entfernen kann. Schritt für Schritt arbeitet auch Lajewski sich weiter vor, um die Komponenten ideal miteinander zu verbinden und eine gebrauchsfähige Rezeptur zu entwickeln.
Beide Projekte stoßen schon jetzt auf großes Interesse in der Industrie. Trotz erster Erfolge liegt vor den Wissenschaftlerinnen noch viel Detailarbeit. Für Geyer ist ihre Forschung ein gutes Beispiel für die „Stellschrauben, die wir drehen können, um zentrale Zukunftsfragen im 3D-Druck wie das Recycling und den Schutz von Ressourcen und Umwelt zu beantworten“.
Text: Jutta Witte
Dr. Alexander Geyer, Institut für Kunststofftechnik, E-Mail, Telefon: +49 711 685 62850