Ein atemberaubender
Crash beim Formel 1 Rennen - doch der Rennfahrer steigt
wenig später unbeschadet aus seiner Maschine. Ohne den so
genannten Crash-Absorber wäre das kaum möglich. Der Absorber
aus einem Verbundstoff mit Kohlenstofffasern zerbröselt beim
Zusammenprall in kleinste Krümel und fängt dadurch rund
fünfmal soviel Energie auf wie ein Stahlträger. Dies ist ein
Grund, weshalb Prof. Klaus Drechsler, Direktor des Instituts
für Flugzeugbau (IFB), die Kohlenstofffaser „Magische Faser“
nennt. |
Und es gibt noch weitere: Faserverbundwerkstoffe sind bis zu
25 Prozent leichter als Aluminium und 50 Prozent leichter
als vergleichbare Stahlstrukturen. Sie machen Großflugzeuge
wie den neuen Airbus A 380 leichter, schneller, sicherer,
ökologisch verträglicher und kostengünstiger. Allerdings
sind die Fasern nicht ganz billig und die Fertigung läuft
zur Zeit hauptsächlich manuell ab. „Wenn die Prozesse der
Herstellung automatisiert werden, wächst das Potential der
Verbundstoffe enorm, sie werden neben Formel 1 Fahrzeugen
zum Beispiel zunehmend auch für die Automobilindustrie
interessant“, erklärt Drechsler, und beschreibt damit
gleichzeitig eine der Hauptaufgaben des am 8. Oktober mit
einem internationalen Fachkolloquium eingeweihten
Faserverbund-technikums am IFB. Gemeinsam mit
mittelständischen Firmen wollen die Wissenschaftler neue
Techniken für die Serienfertigung optimieren. Auch Fragen
zum Recycling und zum Reparaturkonzept müssen noch geklärt
werden.
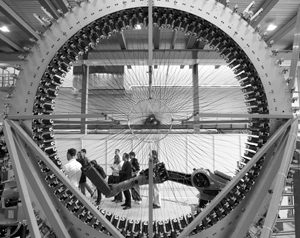 |
|
Besonders beeindruckend im neuen
Faserverbundtechnikum ist die fast fünf Meter hohe
Fle.htmlaschine.
(Foto: Eppler) |
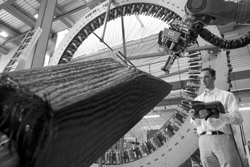 |
|
Unterstützt von einem Roboter werden hier
gleichzeitig 150 Kohlefasern verflochten.
(Foto: Eppler) |
Flugzeugbau und Textiltechnik
Der Trick bei den modernen Verbundwerkstoffen aus
hochfesten Kohlefasern ist, alte Textiltechniken wie Nähen,
Flechten oder Sticken mit neuen Entwicklungen wie
Harzinjektionstechniken oder Mikrowellenhärtung zu
kombinieren. Auf diese Weise kommen die beiden Disziplinen
Flugzeugbau und Textiltechnik zusammen, die auf den ersten
Blick nur wenig Berührungspunkte haben.
Das augenfälligste Element des neuen Faserverbund-technikums
ist die fast fünf Meter hohe Fle.htmlaschine. Sie sieht wie
ein überdimensioniertes Rad eines Fahrrads aus. Statt
Speichen ziehen sich Kohlefasern von außen in die Mitte. Und
dort, wo sich normalerweise die Achse befindet, werden hier,
unterstützt von einem Roboter, gleichzeitig 150 Kohlefasern
verflochten. So entstehen mehrere Lagen Flechtgewebe, die zu
einem drei-dimensionalen textilen Vorformling vernäht werden.
Dieser wird dann mit Harz imprägniert und anschließend
ausgehärtet. Nicht nur Flugzeuge und Autos werden mit den so
gefertigten Hightech-Bauteilen ausgerüstet, auch
Fahrradsattel, Ski und Gebäude profitieren von dem neuen
Werkstoff. Aufgaben für das Technikum und Anfragen von
verschiedensten Firmen gibt es deshalb viele.
Modernes Technikum
„Das Technikum zählt zu den weltweit modernsten Anlagen
dieser Art“, betont Prof. Drechsler. Neben der
Fle.htmlaschine ist es mit weiteren Neuentwicklungen
ausgestattet. Dazu zählt eine Nähanlage, die durch Nähköpfe
mit einer sichelförmig gebogenen Nadel das Nähen nur von
einer Seite ermöglicht. Eine Stickmaschine stellt Gewebe aus
Kohlefasern her und verarbeitet die Fasern entsprechend der
zuvor vom Computer berechneten Belastungen eines Werkstücks,
ohne Verschnitt zu produzieren. Und um das Härten mit
Epoxidharz zu optimieren, entwarfen die Stuttgarter
Wissen-schaftler gemeinsam mit dem Forschungszentrum
Karlsruhe einen speziellen Mikrowellenofen mit einem absolut
homogenen Energiefeld.
Auch Firmen profitieren
Von dem Faserverbundtechnikum profitieren alle
Beteiligten. Gert Wagener, Geschäftsführer der Textilfirma
Saertex, ist überzeugt von dem hohen Potential der
Faserverbundstoffe für viele Unternehmen, „doch die
Forschungsarbeit können vor allem mittelständische Firmen
nicht finanzieren“. So sieht es auch Dr. Janpeter Horn,
Geschäftsführer der Firma Herzog Fle.htmlaschinen: „Wir
brauchen Partner, die uns in der Forschung unterstützen.
Kompetenznetzwerke an den Universitäten sind sehr wichtig.“
Für die Uni bietet sich mit dem Technikum eine „exzellente
Grundlage für die Lehre, die Forschung und die Einwerbung
von Drittmittelprojekten“, ist Prof. Klaus Drechsler
überzeugt. Schon jetzt sind von der Europäischen Union und
dem Bundesforschungsministerium finanzierte Projekte
angelaufen.Doch damit nicht genug, ist für nächstes Jahr die Gründung
eines Kompetenzzentrums für Leichtbau geplant, auch bei
diesem Verbund wird das IFB beteiligt sein. Hierzu laufen
schon Forschungsarbeiten, wie der wissenschaftliche
Mitarbeiter Rainer Kehrle zeigt. So genannte Faltwaben, in
Endlosstrukturen produziert, eignen sich hervorragend für
den Einbau in Flugzeuge. Sie sind sehr leicht und im
Gegensatz zu den herkömmlichen Strukturen kann bei diesen
Faltungen entstehendes Kondenswasser abfließen statt zu
gefrieren.
Birgit Vennemann
KONTAKT
Prof. Dr.-Ing. Klaus Drechsler
Institut für Flugzeugbau
Pfaffenwaldring 31, 70569 Stuttgart
Tel. 0711/685-2402
Fax 0711/685-2449
e-mail:
drechsler@ifb.uni-stuttgart.de
|